Early Thanksgiving
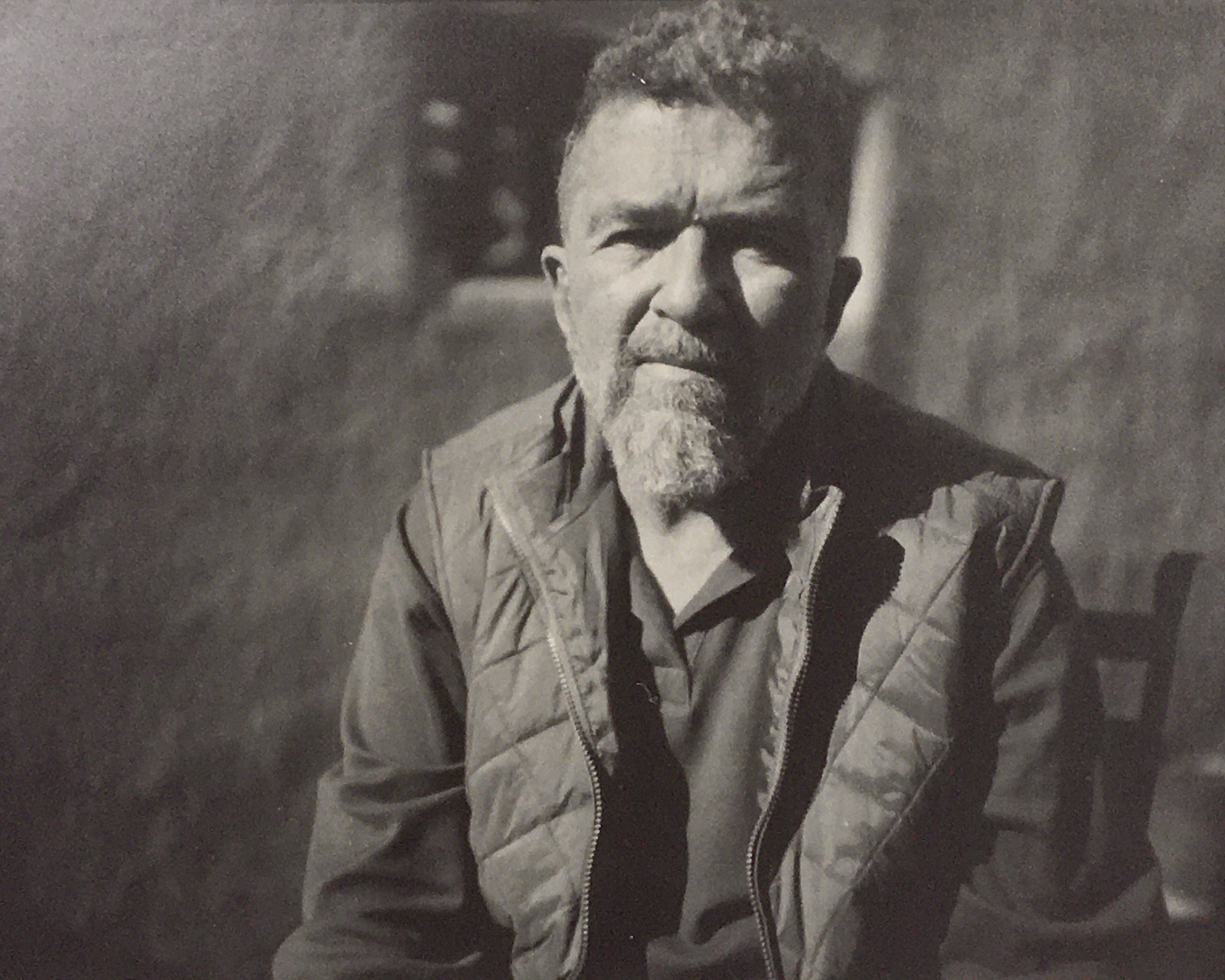

The Cameradactyl OG with Kodak Ektar 127mm F/4.7 lens:

Rear view showing view screen, 1:1 finder and close-up focusing string:
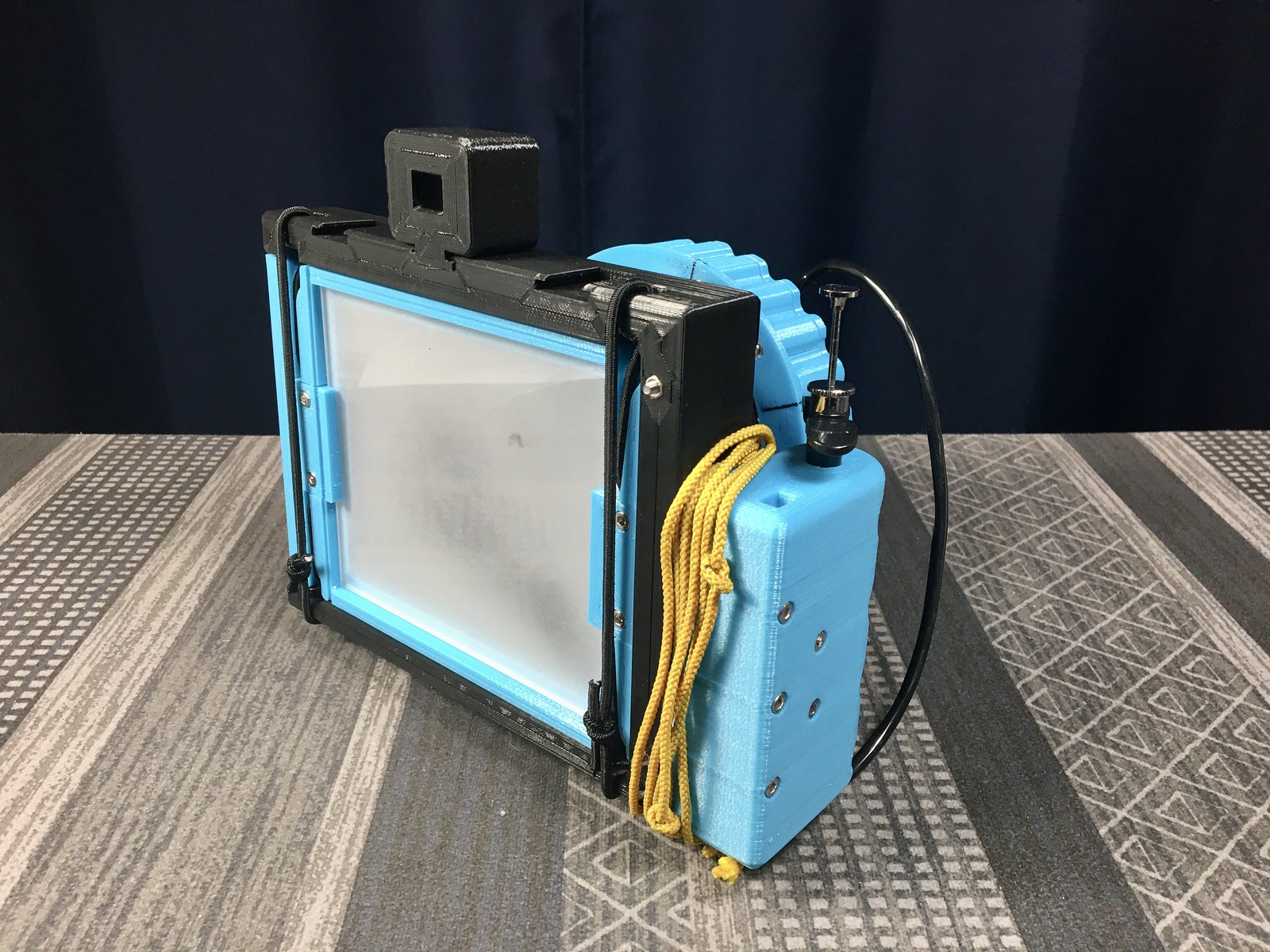
The shutter release cable feeds through a hole in the grip. There's also a slot in the grip for a camera strap.
There are three mounting slots for the 1:1 finder, I prefer the middle slot, to reduce parallax error.
The large blue lens mounting ring up front is also the helical focuser. I have lines marked on the focus ring to indicate infinity focus, along with three closer distances, equivalent to three knots tied in the yellow focusing string.
For the self-portrait at the top, I preset the focus ring for the closest position, then placed the first knot of the string against my temple, adjacent to my eye, then stretched the string taught. A 36" shutter release cable permitted me to trigger the shutter from that position. Exposure was metered at ISO 3 + 3 stops, which came to F/5.6 at 1/2 second in bright sun. The direct positive print was processed using the citric acid / hydrogen peroxide method, using the same chemicals I've been using for a few months.
Here's a close-up of the newly acquired Ektar 127mm lens, with the front ring removed to gain access for degreasing and cleaning. I was able to get the speeds back pretty close to normal, but the bulb position still doesn't work; but I can still use a dark slide over the lens while in the preview mode instead.

Typecast via Torpedo 18:

Labels: Cameradactyl, direct positive process, Kodak Ektar 127mm, Torpedo 18